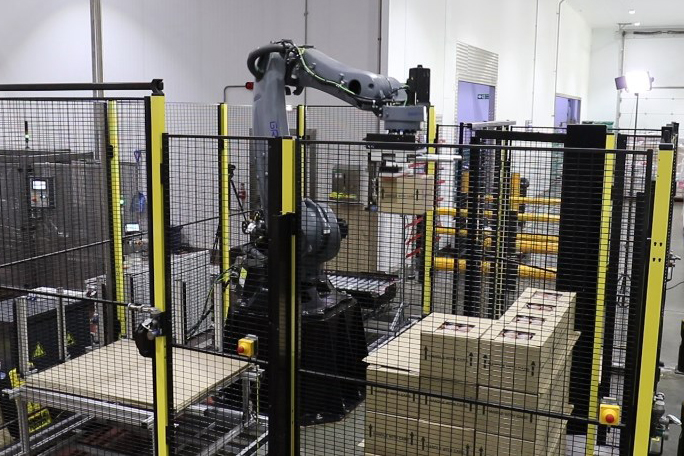
Robotic palletisers are renowned for their exceptional reliability, making them a preferred choice across a wide range of industries. Their advanced technology, precision, and durability contribute to their robust performance. Here’s an in-depth look at the factors that make robotic palletisers reliable:
Precision and Consistency
- High Accuracy: Robotic palletisers excel in placing product on pallets with high precision, ensuring consistent stacking patterns. This accuracy minimises the risk of product damage and enhances overall packaging quality.
- Repetitive Task Mastery: Robots are designed to perform repetitive tasks with exacting consistency. This capability ensures uniform output quality and operational efficiency over extended periods.
Durability and Robustness
- Industrial-Grade Components: Constructed with high-quality, industrial-grade components, robotic palletisers are built to withstand the demanding conditions of industrial environments. This robustness translates to longer operational life and reduced wear and tear.
- Extended Longevity: With proper maintenance, robotic palletisers can provide reliable service for many years, often surpassing a decade of continuous operation.
Low Downtime
- Minimal Maintenance Requirements: Robotic palletisers typically require less frequent and less intensive maintenance compared to conventional palletisers, reducing overall downtime.
- Rapid Diagnostics and Repairs: Equipped with advanced diagnostic tools, robotic palletisers can quickly identify and address issues, minimising the time needed for repairs and maintenance. Systems that have a remote log in functionality for remote support greatly reduce downtime and increase reliability.
Adaptability and Versatility
- Handling Diversity: Capable of managing a wide range of product sizes, shapes, and weights, robotic palletisers can easily adapt to changes in production without significant downtime or reconfiguration.
- Ease of Reprogramming: The programmable nature of a robotic system allows for quick adjustments to palletising patterns or new product lines, enhancing flexibility and responsiveness to market demands.
Advanced Technologies
- Integrated Sensors and Vision Systems: Advanced sensors and vision systems enhance the accuracy and efficiency of robotic palletisers, reducing errors and ensuring precise placement of boxes.
- Seamless Automation Integration: Robotic palletisers integrate smoothly with other automated systems, ensuring synchronised operations and reducing bottlenecks in the production process.
Enhanced Safety Features
- Comprehensive Safety Mechanisms: Equipped with protective enclosures, emergency stop functions, and sensors, robotic palletisers offer enhanced safety for operators and reduce the risk of accidents.
- Reduction in Human Error: Automation significantly reduces the likelihood of human errors that can lead to operational downtime or product damage, further enhancing reliability.
Proven Track Record
- Widespread Industry Adoption: Robotic palletisers have been widely adopted across various industries, demonstrating their reliability and effectiveness in diverse real-world applications.
- Positive User Feedback: Numerous case studies and testimonials from users highlight the robust performance and reliability of robotic palletisers, reinforcing their reputation as a dependable automation solution.
Ensuring Optimal Reliability
- Regular Maintenance: Adhering to a structured maintenance schedule is crucial to keeping robotic palletisers in optimal condition and ensuring their longevity.
- Professional Installation: Proper installation and integration with existing systems by professionals ensure the palletiser operates seamlessly from the start.
- Operator Training: Comprehensive training for operators on the use and troubleshooting of robotic palletisers is essential for maintaining smooth and efficient operations.
- Selecting the Right System: Choosing a robotic palletiser that aligns with specific operational needs, production volumes, and box specifications ensures maximum efficiency and reliability.
Conclusion
Robotic palletisers are a cornerstone of modern automation, providing unmatched reliability through their precision, durability, and adaptability. Their advanced technologies, coupled with a proven track record in many different industries, make them a reliable choice for automating the palletising process. By ensuring regular maintenance, professional installation, and adequate operator training, businesses can maximize the reliability and efficiency of their robotic palletising systems, achieving consistent and high-quality results over the long term.
If you would like to discuss your specific palletising requirements and the best methods of automating your process, please contact us on 01223 499488 or helpline@granta-automation.co.uk and we will be happy to help.
Warning: Undefined variable $aria_req in /var/www/granta-automation.co.uk/news/wp-content/themes/twentyten/comments.php on line 81
Warning: Undefined variable $aria_req in /var/www/granta-automation.co.uk/news/wp-content/themes/twentyten/comments.php on line 86