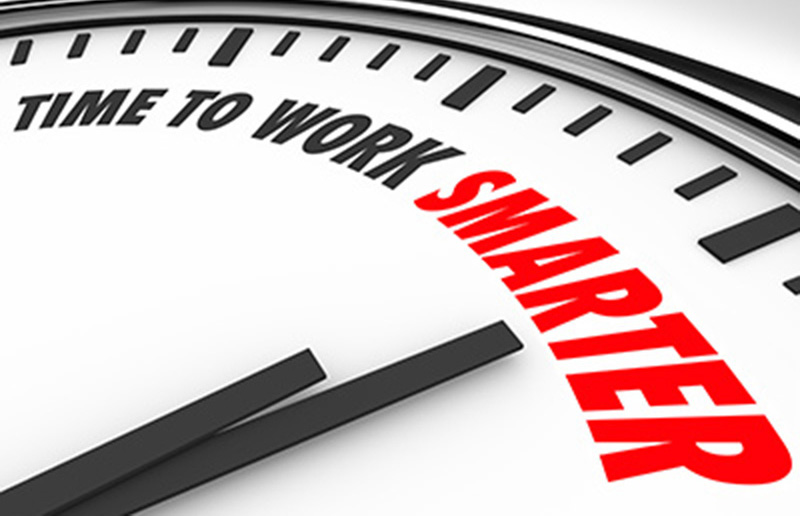
The manufacturing and logistics industries are facing an unprecedented challenge: a shortage of skilled labour. Over the past few years, several factors have compounded this issue, including the global pandemic, an aging workforce, and shifting economic priorities. As demand for goods continues to rise and supply chains become more complex, the struggle to fill open positions and maintain operational efficiency has reached a critical point. We’ll explore the reasons behind this labour shortage, the role automation plays in bridging this gap, how businesses can improve worker retention through better work conditions, and why investing in upskilling and reskilling programs is essential for long-term success.
Why Manufacturing Is Facing a Worker Shortage
Labour shortages in manufacturing and logistics are not new, but they have become more pronounced in recent years due to a combination of global trends and local challenges.
- Aging Workforce: Many workers in the manufacturing sector are aging and approaching retirement. According to a report from the National Association of Manufacturers, over 2 million manufacturing jobs could go unfilled by 2030 due to an aging workforce. The problem is particularly acute in skilled trades, where experience is key. While new technology and automation are rapidly transforming industries, the workforce isn’t keeping up with the technical skills needed to manage these systems.
- Pandemic Disruptions: The COVID-19 pandemic disrupted global supply chains and forced many manufacturing plants and warehouses to shut down temporarily. During this period, many workers were furloughed, laid off, or decided to exit the workforce due to health concerns, childcare responsibilities, or a re-evaluation of career goals. As the world has gradually reopened, many industries are struggling to bring employees back at the same levels. This is especially true in manufacturing, where production has not fully rebounded in some areas.
- Attraction to Other Sectors: As manufacturing and logistics sectors compete with other industries for workers, many potential employees are gravitating towards fields that offer higher wages, more flexibility, and perceived better work conditions. Retail and tech companies, in particular, have attracted younger, more tech-savvy workers, leading to further gaps in the workforce that are difficult to fill.
The Role of Automation in Filling Labour Gaps
While the labour shortage presents significant challenges, the increased use of automation in manufacturing and logistics offers a solution. Far from being a replacement for human workers, automation fills the gaps where labour shortages are most pronounced, complementing the workforce and boosting overall productivity.
- Handling Repetitive and Labour-Intensive Tasks: One of the greatest advantages of automation is its ability to take over repetitive, manual tasks that are often physically demanding. Tasks like palletising, packaging, sorting, and material handling, which would traditionally require a significant labour force, can now be managed by robotic systems. This allows companies to keep production moving even when human resources are stretched thin.
- Increased Efficiency and Reduced Downtime: Automation systems, such as robotic arms and conveyor belts, can work 24/7 without the need for breaks, eliminating downtime that often occurs due to labour shortages. Machines perform tasks with high precision, eliminating human error and minimising waste, which leads to improved operational efficiency.
- Filling Labour Gaps in Critical Areas: Labour shortages can affect specific shifts or high-demand times, such as during peak seasons or when production quotas need to be met. Automation can be deployed strategically to fill these gaps—providing scalable solutions for businesses that need to boost productivity without hiring additional staff. For example, during times when warehouse operations are at full capacity, automated storage systems and robots can handle the increased load.
- Cost-Effectiveness in a Changing Economic Landscape: The upcoming National Insurance (NI) increases in April present additional financial pressure on employers. These changes are expected to increase the overall cost of hiring, further highlighting the financial burden of a large, full-time workforce. While automation does require an initial investment, it offers long-term savings by reducing reliance on human labour and lowering operational costs. When factoring in wage increases, benefits, and administrative costs, automation becomes a highly cost-effective solution for many manufacturers and logistics providers, helping to offset these rising expenses. This makes automation an even more attractive option in the current economic climate, enabling businesses to remain competitive and continue scaling.
Attracting and Retaining Talent Through Better Work Conditions
Although automation offers significant benefits, human workers remain integral to operations, particularly in roles requiring technical expertise, strategic decision-making, and creative problem-solving. To retain and attract talent in today’s competitive labour market, businesses must offer work environments that prioritise employee well-being, growth, and job satisfaction.
- Competitive Compensation and Benefits: While wage competition continues to rise, companies must also focus on offering a benefits package that supports employees’ long-term health and financial security. Health insurance, retirement plans, paid time off, and wellness programs are important incentives. Additionally, providing bonuses and performance incentives can help attract top talent, especially in roles that require specialised skills.
- Workplace Flexibility: One of the most attractive benefits for employees in today’s workforce is flexibility. While manufacturing and logistics roles can be more challenging to offer remote work options, offering flexible shift scheduling, part-time opportunities, or even compressed work weeks (e.g., four-day work weeks) can provide workers with a better work-life balance. These adjustments can improve employee satisfaction and reduce burnout, ultimately helping with retention.
- A Safe, Healthy, and Modern Work Environment: Workers want to feel safe, comfortable, and valued in their jobs. Investing in ergonomic workplace designs, updated safety protocols, and advanced machinery to reduce physical strain can create a positive work environment. Additionally, embracing clean, modern facilities demonstrates a commitment to employee welfare, which not only boosts morale but also enhances productivity.
- Clear Career Advancement Paths: The best way to retain top talent is to offer them opportunities for growth. Career development programs that include mentorship, clear career paths, and access to professional development training help employees feel valued and invested in the company’s success. Investing in employee growth through leadership training programs also strengthens internal talent pipelines and prepares your business for long-term success.
Upskilling and Reskilling the Workforce
As automation continues to transform manufacturing and logistics, it’s more important than ever to invest in upskilling and reskilling programs. While automation handles many tasks, human workers are still needed to manage and maintain advanced systems, troubleshoot issues, and drive innovation.
- Training and Certification Programs: Offering employees opportunities to learn new skills and stay up-to-date with the latest technological advancements ensures that your workforce remains agile and adaptable. Whether through in-house training, online courses, or partnerships with technical colleges, equipping your workers with the necessary skills to operate advanced machinery and automated systems will help your business stay competitive.
- Cross-Training and Job Rotation: By cross-training employees, you increase flexibility and versatility within your workforce. Employees can be shifted between different tasks based on demand, which helps reduce bottlenecks and ensures that production lines continue running smoothly, even during peak periods.
- Building a Strong Leadership Pipeline: Leadership is a critical component of any organisation, especially as automation technologies grow more complex. Training the next generation of leaders—those who can manage both human and robotic systems—is vital for future success. Providing leadership development programs that focus on both technical and managerial skills will help you build a capable team that can guide your company through ongoing technological changes.
Labour shortages in manufacturing and logistics present a significant challenge, but they are not without solutions. A combination of automation, better working conditions, and a focus on workforce development offers a pathway forward. Automation plays a key role in bridging labour gaps, enhancing efficiency, and controlling costs, especially with economic shifts on the horizon. However, it’s important to view automation as a complement to human workers, not a replacement, fostering a more productive and adaptable workforce. By prioritising both automation and talent retention, companies in manufacturing and logistics can build a more resilient and sustainable workforce, positioned to succeed in a competitive market.
If you would like to know more about the Granta palletising systems or AMR/AGV systems, then please do get in touch on 01223 499488 or contact us at helpline@granta-automation.co.uk. We will be very happy to help.
Find out more…
- Ways To Speed Up The Palletising Process In Production
- How To Automate Cross Palletising and Depalletising from UK to Euro Pallets
- How Cycle Time Reduction Improves Operational Efficiency
- Autonomous Mobile Robot (AMR) Pallet Stations, Charging Stations, and Conveyor Stations
- Mastering Budget Planning: Advanced Methods for Planning and Allocating Capital Budgets in Manufacturing
Warning: Undefined variable $aria_req in /var/www/granta-automation.co.uk/news/wp-content/themes/twentyten/comments.php on line 81
Warning: Undefined variable $aria_req in /var/www/granta-automation.co.uk/news/wp-content/themes/twentyten/comments.php on line 86