Automated palletisers offer several advantages and disadvantages. However, each automated palletising application is unique, so there may be other advantages or disadvantages applicable to your situation that are not listed here. Below are some of the key advantages and disadvantages of automated palletisers:
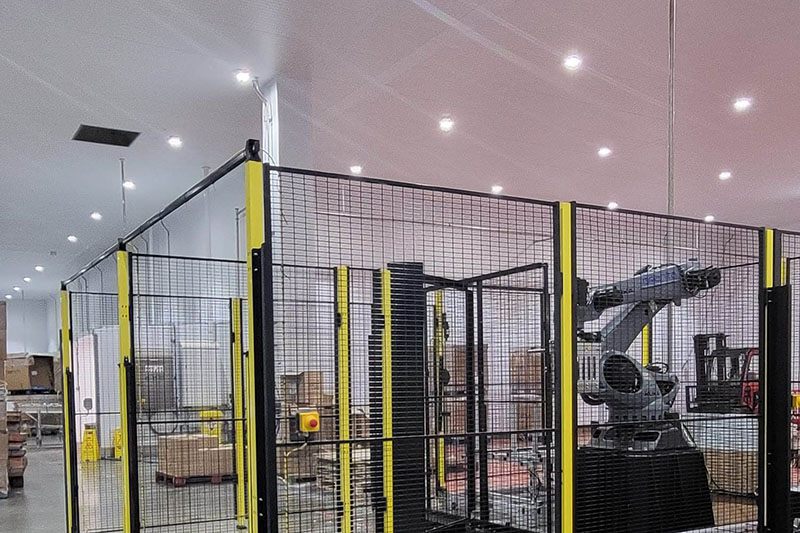
Disadvantages of Automated Palletisers:
Some of the key disadvantages of automated palletisers are listed below, however depending on the type of system you purchase and the company you purchase from, these disadvantages may not all apply.
- High Initial Investment: Implementing an automated palletizing system typically requires a significant upfront investment. The cost includes purchasing the equipment, installation, and integration with existing infrastructure. For small businesses or those with limited budgets, this initial investment may be a deterrent. However, automated palletising systems are also available on leasing schemes which eliminates the requirement for any initial capital outlay.
- Maintenance and Technical Support: Automated palletisers require regular maintenance to ensure optimal performance. They have complex mechanical and electrical components that may require specialized knowledge or technical support for repairs. Businesses need to budget for ongoing maintenance costs and have access to trained personnel or reliable service providers. Typically, an automated palletising solution will come with a support contract in place to ensure that the system is regularly checked and maintained.
- Limited Flexibility for Irregular Products: While automated palletisers offer flexibility for a wide range of products, they may have limitations when it comes to irregularly shaped or fragile items. Certain products may not fit within the standard parameters of the palletiser, requiring manual intervention or alternative palletising methods.
- Initial Setup and Programming: Setting up an automated palletising system and programming it to accommodate specific products and stacking patterns can be time-consuming. It may require technical expertise and thorough testing to ensure the system operates efficiently. Changes in product specifications or stacking requirements may also require reprogramming, which can lead to downtime and temporary disruptions. However, there are palletising systems on the market that have easy programming software as standard, enabling your factory staff to reprogram the robot for different product sizes quickly and easily.
Advantages of Automated Palletisers:
Automated palletisers have many different advantages, and the benefits for your company will be determined by your palletising requirements and how these will be met. However, some of the more common advantages are listed below.
- Increased Efficiency: Automated palletisers can significantly improve the efficiency of palletising operations by handling high volumes of products at a faster rate compared to manual labour. They can work continuously without the need for breaks, resulting in increased productivity.
- Consistency and Accuracy: Automated palletisers ensure consistent and accurate pallet stacking, minimising errors and reducing the risk of damaged products during transportation. They can precisely position each item according to the predefined stacking pattern, optimizing space utilization.
- Reduced Labor Costs: By automating the palletising process, businesses can reduce their reliance on manual labour. This can lead to significant cost savings in the long run, as automated systems require less manpower, no breaks, and eliminate the need for manual lifting, which therefore reduces the risk of workplace injuries occurring.
- Flexibility and Adaptability: Many automated palletisers are designed to handle a wide range of product types, sizes, and weights. They can be easily programmed by factory staff for different product sizes, and auto generate optimised stacking patterns to choose from; making them suitable for diverse industries and applications. This flexibility allows businesses to adapt to changing production requirements and market demands more effectively.
- Integration with Production Lines: Automated palletisers can be seamlessly integrated with other production line equipment, such as conveyor systems, sorting machines, and packaging equipment. This integration enables a smooth flow of products from manufacturing to palletising to shipping, eliminating bottlenecks and optimising the overall production process.
Whilst these are some of the more common advantages and disadvantages of automated palletisers, it is important for businesses to evaluate their specific needs, production volumes, and budget constraints before deciding whether to invest in an automated palletising system.
You may find the following tools useful when analysing the advantages and disadvantages of automated palletising for your specific application:
- Automation Project Payback Calculator – https://www.granta-automation.co.uk/automation-project-payback-calculator
- Intangible Benefits Calculator – https://www.granta-automation.co.uk/news/how-to-define-the-value-of-intangible-benefits/
You may also wish to complete a budget quote request on our project builder to get an understanding of what an automated palletising solution will cost for your specific application. Simply fill in the details and we’ll get back to you with budget pricing within 24 hours. https://www.granta-automation.co.uk/project-builder
If you would like to discuss your specific application in more detail then feel free to contact us on 01223 499488 or helpline@granta-automation.co.uk and we will be very happy to help.
Warning: Undefined variable $aria_req in /var/www/granta-automation.co.uk/news/wp-content/themes/twentyten/comments.php on line 81
Warning: Undefined variable $aria_req in /var/www/granta-automation.co.uk/news/wp-content/themes/twentyten/comments.php on line 86