It is a common requirement both at distribution centers, and on the output of production lines, to need to sort products and palletise them ready for dispatch. Some common requirements include:
- Sorting and palletising into van/delivery routes
- Sorting and palletising by barcode
- Sorting and palletising into product types
- Sorting and palletising by product weight
- Sorting and palletising by size
- Sorting and palletising by customer order number
Key information required for product sorting
Almost any product can be sorted and palletised including boxes, totes, trays, bags and much more, but there is some key information that is required to be considered first:
- What products need sorting?
- Are they consistent, or a range of different types and sizes?
- What speeds do they need sorting at?
- What is the input to the system; is it multiple lines that need combining and sorting, or one line that needs splitting and sorting?
- How many sorted output pallets need to be stacked at one time?
What is the method for detection for how products should be sorted?
There are several methods by which products can be sorted, some examples are below:
- Barcode – Barcode readers detect the barcode and sort according to data from a database or pre-set program.
- QR code – QR code readers detect the code and sort according to data from a database or pre-set program.
- Size measurement – In-line 3D measuring systems can detect product sizes and sort accordingly.
- Weight measurement – Scales in line with the input to the system can weigh products and then sort them accordingly.
- Character recognition off a label – Vision systems can detect the code and sort according to data from a database or pre-set program.
Sorting and palletising methods
Products can be sorted in multiple ways, typically you have products entering the system on a conveyor combined together and they are detected and allocated for sorting to the correct pallet by one of the above sorting methods. Once this allocation is made the products need to be sorted physically and palletised. The key methods for sorting and palletising are as follows:
- Sorting with the robotic palletiser
- Sorting with conveyors then palletising
- Sorting with a buffering system
These are explained in more detail below.
Sorting with a robotic palletiser
Sorting with a robotic palletiser is where the input conveyor to the palletiser has mixed products that need sorting. The palletiser has multiple palletising locations and stacks the products onto the relevant pallet.
For example, the image below shows two sorting Palletisers both stacking to six output pallets; so overall the system is sorting and palletising products between twelve different pallets.
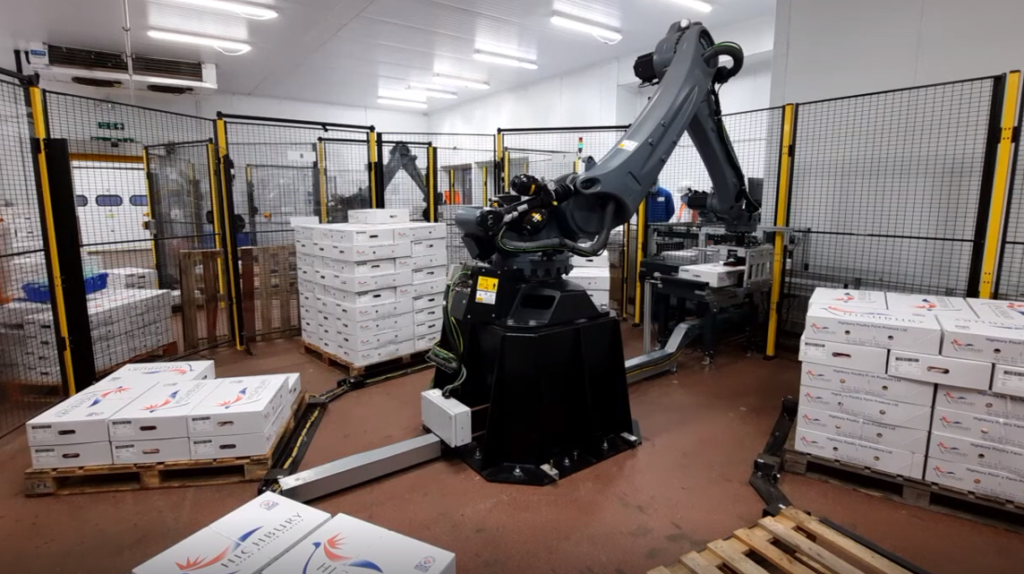
Sorting with conveyors then palletising
Sorting with conveyors is where products are diverted off into different lanes going to the palletiser, this means products are already sorted and combined on input lanes into the palletisers. This is more common where there is high production throughput and products need to be pre-sorted before the palletiser to enable row grip (multi picking products to improve production speeds).

Sorting with a buffering system
Sorting with a buffering system is often effective where there are many different output pallets required but overall production is not all that fast. With this type of system the products are all sorted and stored temporarily in elevated storage systems into batches of product ready to be palletised once a whole pallet worth of product is ready. Like this you can often have just one or two robots serving a large sorting requirement.

Database integration
Often to sort most effectively the barcode or QR code information needs to be looked up on an existing customer database system. To do this the palletising system is integrated using bespoke coding that links up with client databases or imports excel / CSV outputs from client databases. The system then uses this information to determine the sort method and palletise.
If needed, feedback to the database can be given from the palletiser and sorting system to show any extra information from the product; giving real time information on where products are in the system and where products have been stacked. For example; often a barcode reader in the final palletising cell is used to verify the products have been palletised and is used as the method of scanning the product out of the system for delivery.
Conclusion
There are multiple methods of sorting and palletising and often these methods are combined along with database integration to achieve the best outcome. For help with your specific sorting and palletising requirements contact us on 01223 499488 or helpline@granta-automation.co.uk.
Warning: Undefined variable $aria_req in /var/www/granta-automation.co.uk/news/wp-content/themes/twentyten/comments.php on line 81
Warning: Undefined variable $aria_req in /var/www/granta-automation.co.uk/news/wp-content/themes/twentyten/comments.php on line 86