Yes, a single robot can effectively palletise products from multiple production lines onto multiple pallet locations – watch the video below.
This capability can significantly enhance operational efficiency and flexibility in manufacturing settings. Here’s how it can be accomplished:
How It Works:
- Advanced Programming: The robot is equipped with sophisticated programming that enables it to recognise products from different lines and understand where each product needs to be placed. This involves mapping out the exact positions of incoming products and their designated pallet location.
- Integrated Conveyor System: Multiple conveyor belts are used to transport products from various production lines to a central pick-up area. This setup ensures that the robot can access products from all lines without needing to move extensively.
- Vision Systems and Sensors: The robot employs advanced vision systems and sensors to identify and differentiate products. These systems help the robot determine the size, shape, and type of each product, ensuring accurate and efficient handling.
- Gripper design: The robot’s gripper is designed to suit the variety of product types that need to be handled, such as boxes and trays. To maintain efficiency, the gripper will typically be designed to enable it to lift all of the different product types required, as gripper change overs during the palletising process reduce cycle time and efficiency.
Practical Steps:
- Conveyor Design: The conveyor system is designed to converge products from different lines into a central location that the robot can easily access. This reduces the need for multiple robots and simplifies the overall layout.
- Strategic Robot Positioning: The robot is then placed in a central position where it can reach both the convergence point of the conveyor belts and the palletising area efficiently. This strategic placement minimises the robot’s movement and maximises its productivity.
- Safety Measures: Safety measures such as sensors, barriers, and emergency stops are integrated into the system to ensure safe operation. These measures protect workers and equipment, creating a safe working environment.
Example Workflow:
- Product Convergence: Products from different production lines are transported via conveyor belts to a central pick-up area.
- Product Identification: The robot uses its vision systems and sensors to identify each product and determine which line it came from and where it needs to be placed.
- Pick-and-Place Operation: The robot automatically calculates motion paths using AI, and palletises according to lane priority. Efficiently picking and placing products one by one, or in multiples.
Benefits:
- Increased Efficiency: By handling multiple lines with a single robot, the system reduces the need for multiple palletising setups, thereby streamlining operations and saving valuable floor space.
- Cost Savings: Utilising one robot instead of multiple robots and associated equipment significantly cuts down on capital expenditures and operational costs.
- Enhanced Flexibility: The system can easily adapt to changes in production lines and product types, providing a versatile solution that can handle a wide range of palletising tasks.
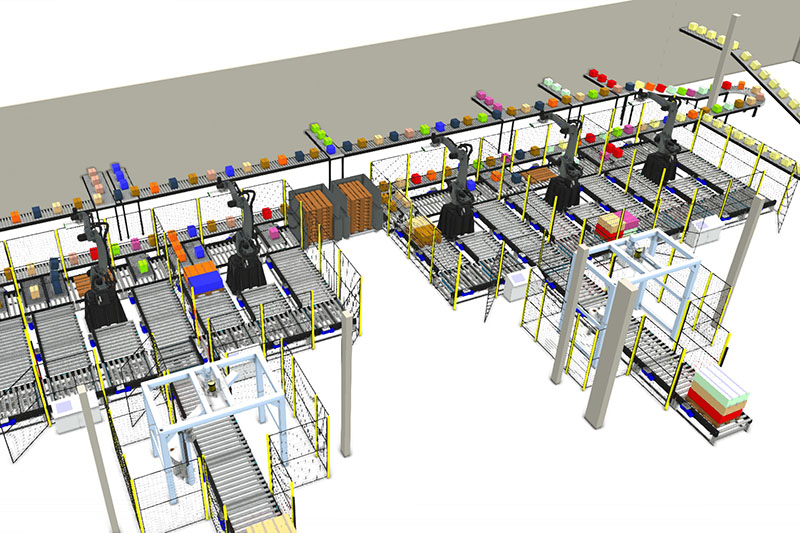
For more information, or to discuss you specific applications, contact us on 01223 499488 .
Warning: Undefined variable $aria_req in /var/www/granta-automation.co.uk/news/wp-content/themes/twentyten/comments.php on line 81
Warning: Undefined variable $aria_req in /var/www/granta-automation.co.uk/news/wp-content/themes/twentyten/comments.php on line 86