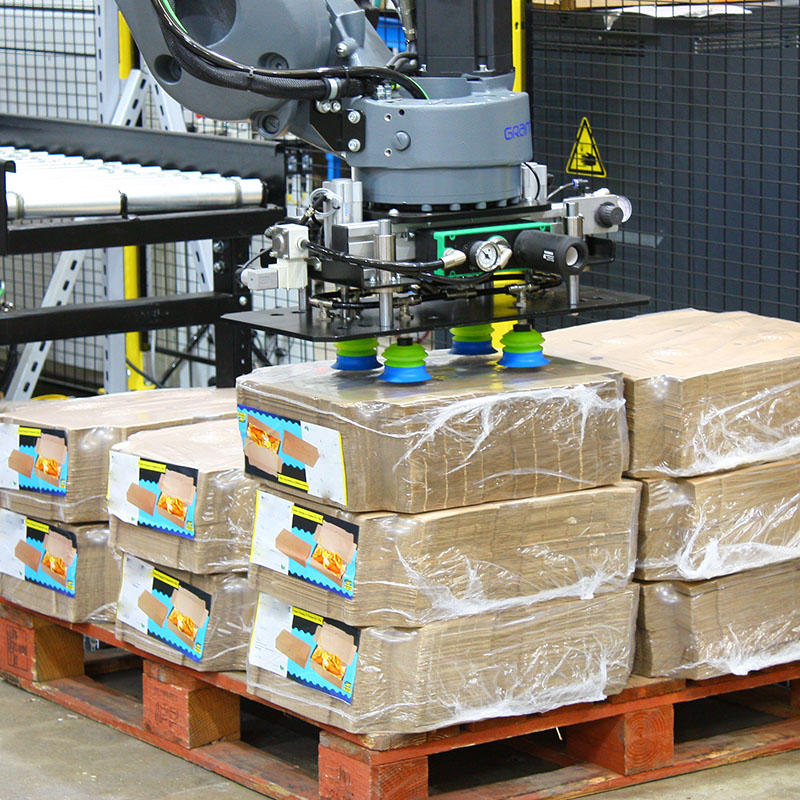
Cross palletising of product from Euro to UK pallets, or UK to CHEP pallets, is a task that is becoming more frequently required than ever before. With the advances in robotic systems and easy programming software, automating this process has now become a very viable option, resulting in enhanced productivity, reduced labour costs, and eliminating human error.
Understanding The Implications of Repalletising
Before diving into the robotic system and how it works, it is important to understand the implications of transferring from one pallet type to another. The difference in pallet size means that products must be rearranged and restacked, usually in a different stack pattern, to fit onto the new pallet. This means that depending on the layout of the goods, they may be able to be removed in multiples, or they may need to be removed individually.
How do Robotic Systems Cross Palletise and Depalletise Product
In essence, a robotic system will pick product form one pallet and place it onto another, however, below is a more detailed explanation of how such a system typically operates:
- Detection and Analysis:
- The system is programmed for the product size that is being depalletised and the correct stack pattern for repalletising on the destination pallet is selected. With easy programming software on the palletiser this is very quick and easy to do.
- If required the system can also use advanced sensors, cameras, and detection tools to scan and pinpoint the exact layout and positioning of items on the source pallet.
- Utilising sophisticated software algorithms, it analyses the gathered data to determine the optimal sequence and method for efficiently picking up each item
- Depalletising:
- The robotic arm selects and securely grips each item on the source pallet. Typically, a vacuum gripper would be used, but other gripper types may be used depending on the product type.
- The robotic arm then lifts each item from the source pallet with precision. Depending on the nature and layout of the product being depalletised, product may be lifted individually or in multiples.
- An angled alignment frame or conveyor system may be used to ensure the product is accurately re-positioned prior to repalletising onto the new pallet.
- Repalletising:
- The robotic arm then moves each item (or multiples of items) from the source pallet to the destination pallet. Items are then strategically placed onto the destination pallet in the pre-selected stack pattern.
- This process is then repeated until all of the items on the source pallet have been successfully transferred.
Products best suited to automated depalletising systems
Some products are better suited to automated depalletising than others. Below is a list of product types that typically work well on automated depalletising and repalletising systems.
- Cartons and Boxes: Automated systems can be efficiently used to depalletise cartons and boxes of various sizes and weights. This is commonly used in distribution centres, and e-commerce warehouses. A vacuum gripper is typically used for this task.
- Bottles and Containers: Automated systems can be used to depalletise bottles, jars, cans, and containers in industries such as food and beverage and pharmaceuticals. A bespoke gripper would typically be used for this, and it would be designed to specifically suit the type of bottle/container being depalletised.
- Palletised Drums: Industries dealing with chemicals and oils use automatic depalletisation for handling palletised drums. A barrel gripper with two clamping arms is typically employed for secure handling of drums and barrels.
Key Benefits of Using Robotic Systems for Depalletising and Cross Palletising
There are many different benefits of using an automated system for depalletising and cross stacking of pallets. Listed below are some of the key benefits.
- Increased Efficiency: Robotic systems operate continuously and can handle high volumes of pallets with minimal downtime.
- Enhanced Precision: Advanced vision systems and precise robotic arms ensure accurate handling and stacking of products, reducing the risk of damage.
- Cost Savings: Automation reduces labour costs associated with manual palletising and depalletising tasks.
- Scalability: Robotic systems can be scaled up or down based on the facility’s needs, making them suitable for operations of all sizes.
- Improved Safety: Automation minimises the need for manual lifting and handling, reducing the risk of workplace injuries and RSI occurring.
Conclusion
By automating depalletising and cross stacking of pallets, businesses can achieve greater efficiency, reduce costs, and improve overall operational safety. These systems eliminate the need for labour-intensive manual handling and reduce the risk of RSI injuries occurring, ensuring a seamless transition between different pallet types. As technology continues to advance, these systems will no doubt become increasingly essential in maintaining competitive and efficient supply chain operations.
If you would like to know more about the Granta depalletising and repalletising systems, then please do get in touch on 01223 499488 or contact us at helpline@granta-automation.co.uk. We will be very happy to help.
Warning: Undefined variable $aria_req in /var/www/granta-automation.co.uk/news/wp-content/themes/twentyten/comments.php on line 81
Warning: Undefined variable $aria_req in /var/www/granta-automation.co.uk/news/wp-content/themes/twentyten/comments.php on line 86