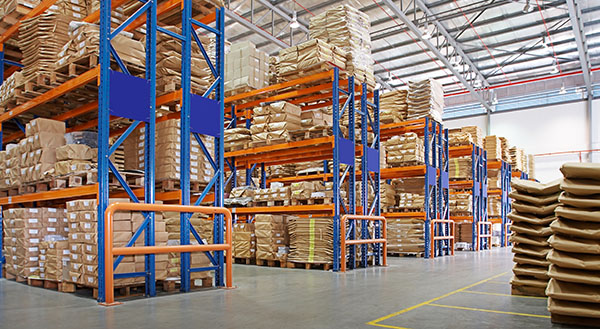
In today’s fast-paced logistics and supply chain environment, palletising plays a pivotal role in determining the overall efficiency, safety, and success of warehousing and distribution processes. Whether handling high-volume shipments or delicate products, businesses must focus on both the accuracy and productivity of their palletising operations to reduce errors, cut costs, and boost throughput. As global demand increases, so does the need for faster, more reliable, and cost-effective palletising solutions.
This article explores four key areas that can drastically enhance palletising operations: increasing palletising accuracy, boosting productivity, implementing efficiency-enhancing techniques, and improving pallet loading speed. Each of these elements is crucial for creating a seamless and high-performing palletising process that supports your business goals and improves the bottom line.
1. Increase Palletising Accuracy
Accuracy in palletising is more than just ensuring that products fit on a pallet. It is about ensuring the safe and secure stacking of goods, preventing damage during transport, and enhancing downstream operations such as storage and delivery. Inaccurate palletising can lead to costly product damage, shipping delays, and even workplace accidents.
To improve palletising accuracy, consider the following:
- Leverage Automation and Robotics: Automated palletisers, particularly robotic systems, have transformed how pallets are loaded. Unlike manual operations, which can be prone to fatigue and human error, automation delivers consistent accuracy and reliability, minimising costly mistakes and product misplacements.
- Regular Maintenance of Equipment: Even the most advanced palletising systems require regular maintenance to maintain peak performance. Worn-out or malfunctioning machinery can compromise accuracy, resulting in poorly stacked or unsafe pallets. Developing a preventive maintenance schedule ensures your equipment remains accurate, preventing costly delays and safety hazards.
- Comprehensive Staff Training: Human oversight is still a vital part of the palletising process, particularly in environments where manual and automated systems coexist. Ensuring that operators are well-trained in monitoring automated systems, making adjustments, and troubleshooting issues helps reduce errors, leading to higher palletising accuracy.
2. Boost Palletising Productivity
In the competitive world of logistics, productivity is key. The faster you can accurately palletise goods, the more efficiently you can move products through your supply chain, reduce lead times, and satisfy customer demands. Boosting productivity doesn’t mean cutting corners—it means smartly integrating technologies and processes that help you do more in less time while maintaining high standards.
Here are strategies for boosting palletising productivity:
- Integrate Conveyor Systems or AGVs/AMRs for Seamless Flow: Conveyor systems or AGVs/AMRs can be a game-changer for speeding up palletising operations. By automating the movement of products from one station to another, you eliminate the need for manual handling, reducing bottlenecks and accelerating the palletising process. Products flow smoothly from production lines to their final destination, optimising throughput and minimising downtime.
- Optimise the Workflow Layout: Take a critical look at your palletising station layout. Ensure that the workflow is designed to minimise unnecessary movements, reduce handling times, and allow easy access to both products and palletising equipment. Streamlined workflows make it easier for palletisers, both human and robotic, to operate at maximum capacity without delays caused by poor design or layout inefficiencies.
- Utilise Easy Programming Software: Easy programming software can automatically calculate the most efficient stacking patterns based on product dimensions, weight distribution, and stability needs, reducing guesswork and manual adjustments.
3. Palletising Efficiency Tips
Efficiency is the key to a well-oiled palletising operation. It is a combination of speed, accuracy, and smart resource allocation. When palletising is done efficiently, it results in lower operational costs, reduced labour requirements, and enhanced productivity.
To increase efficiency, implement the following tips:
- Custom Pallet Patterns for Stability: Every product is unique, and so are its palletising needs. Custom pallet patterns ensure that products are stacked in the most space-efficient and stable manner. By optimising pallet patterns based on product size, shape, and weight, you not only maximise the number of products that fit on a pallet but also reduce the risk of product damage in transit.
- Reduce Manual Intervention with Automation: Manual intervention, though necessary in some scenarios, often leads to slowdowns and potential errors. By automating key steps in the palletising process, you can improve both speed and accuracy. Automated palletisers require less human involvement, freeing up labour for other tasks while maintaining consistency in the palletising process.
- Real-Time Monitoring and Analytics: Efficient palletising operations rely on data. By using real-time performance tracking tools, you can monitor key metrics such as cycle times, error rates, and equipment downtime. This data-driven approach allows you to spot inefficiencies, identify bottlenecks, and make informed decisions that enhance overall palletising performance.
4. Improve Pallet Loading Speed
Speed is a critical factor in palletising operations, especially for businesses that deal with large volumes of shipments. Improving pallet loading speed ensures that goods are processed, loaded, and shipped in a timely manner, meeting customer expectations and maintaining a smooth supply chain.
To improve pallet loading speed, consider these approaches:
- Invest in High-Speed Robotic Palletisers: High-speed palletising robots are designed to handle higher volumes of products in less time without sacrificing accuracy. These robots can work around the clock, stacking products faster than human labour, making them ideal for operations that require quick turnaround times and consistent performance. Row gripping technology is often used where higher speeds are required, picking and placing rows of product at a time, therefore improving cycle time.
- Easy Programming Software to Improve Set Up Time: Easy programming software typically features intuitive, user-friendly interfaces with drag-and-drop functionality or graphical programming. This allows operators to create palletising patterns and routines in minutes without needing in-depth programming knowledge. Some easy programming software will auto generate stack patterns and you can simply select the stack pattern you require.
- Minimise Downtime with Predictive Maintenance: Equipment downtime can drastically affect pallet loading speed. By implementing a predictive maintenance program, you can catch potential issues before they lead to breakdowns. This proactive approach minimises unplanned downtime, ensuring that your palletisers are always running at peak performance.
Through a combination of smart technology investments, strategic workflow enhancements, and a focus on both speed and precision, palletising can become a powerful driver of operational success, cost savings, and customer satisfaction in any warehouse or supply chain environment.
If you would like to know more about the Granta palletising systems, then please do get in touch on 01223 499488 or contact us at helpline@granta-automation.co.uk. We will be very happy to help.
Warning: Undefined variable $aria_req in /var/www/granta-automation.co.uk/news/wp-content/themes/twentyten/comments.php on line 81
Warning: Undefined variable $aria_req in /var/www/granta-automation.co.uk/news/wp-content/themes/twentyten/comments.php on line 86