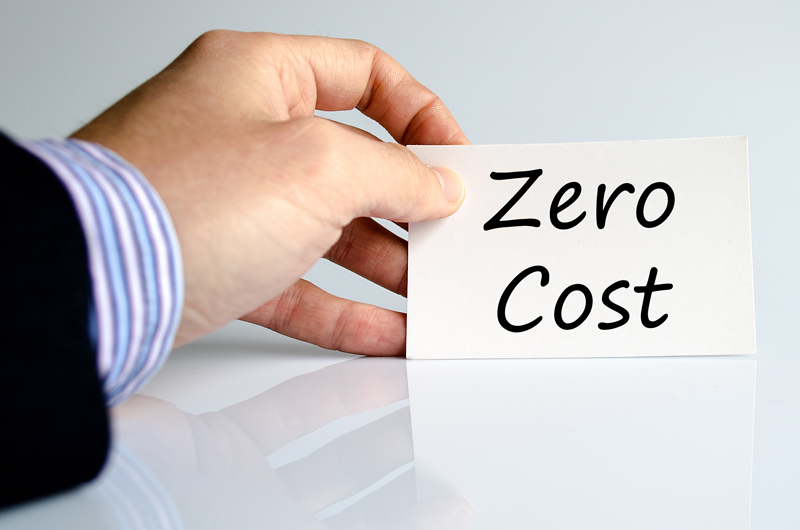
Boosting factory output is something that every manufacturing company wants to do as increased output directly translates into increased profits. However, this can often require capital investment, increased staff costs, and increase overheads, which all start to eat into that extra profit you can make by increasing your factory output.
Here we look into some zero cost ways that you can boost your factory output.
Track OEE
OEE (Overall Equipment Effectiveness) is a calculation that can be done to show exactly how effective your machinery or factory is. It takes into account the speed at which the machine or factory runs, the quality of the finished products produced and the actual machine operating time versus the available operating time. OEE is best calculated per machine rather than across the whole factory as it is then easier to identify where improvements need to be made to help improve productivity. An OEE calculator can be downloaded from here.
Once you have identified the OEE of your machinery, you will then be able to identify which parts of your process aren’t running at full efficiency. This will enable you to put measures in place to reduce or eliminate the inefficiencies, and thus improve the efficiency of your machinery.
Hold Daily Improvement Meetings
Daily improvement meetings are key to increasing employee engagement and creating an ownership mentality amongst your staff. Hold a daily whole team huddle and ask each of your staff to name an improvement they made the day before, or to make an improvement suggestion. Don’t limit your staff to just the area they work in, and don’t penalise them if they don’t have an idea to mention for a day or two. What you will find as a result from these daily meetings is that your staff start to take ownership for improving the business and driving better results. They become motivated by the part they have to play in the big picture of improving the business and they enjoy seeing their suggestions taken up. Often you will find that given the ‘rope’ to run with, your staff will come up with some very innovative and creative ways of improving processes.
Some of the ideas that come up in these meetings may also cause you to question some of your processes, and whether they are necessary, or duplicative. This is something that you can then investigate further outside of your daily team meetings.
Brainstorm With Employees
Hold a brainstorm session with your employees on how to boost your factory output. You will find that as your employees are working on the ‘coal face’, they will often have a different view to you as to what is restricting production output, and given the right forum they will often come up with innovative ways to solve these challenges. It may be a machine that’s always stopping, or a process that is not working properly so the process has to be done twice to achieve the desired result. All too often staff working on the factory floor will just work around inefficiencies in the process, and as a manager you may not even be aware of them. That is why it’s so beneficial to give your staff the forum to share their knowledge of these inefficiencies and to work together with them to find solutions.
Create A Daily Scoreboard
Everyone plays to win, and if you want your staff to play their best, they need to know if they’re winning. Involve your staff in creating daily personal or small team targets for their area of the production process. Their targets must be something that is directly influenceable by them, and achievable, otherwise it won’t have a motivating effect. If your staff have had part in creating the target there will be a far higher buy in than if the targets are forced on them.
Once you’ve agreed the targets, all you need is a piece of paper and a pen to create a scoreboard. Depending on the type of target you have agreed, all you need to then do is to update the scoreboard daily or hourly so that you staff can see exactly where they are in relation to their target. You will find that as you staff see their score going up and they can see their success, the pace will speed up and your production output will increase.
Identify Bottlenecks
Identifying and eliminating bottlenecks in your production process is key to improving output. Information on how to identify bottlenecks in your production process is available here. Once you have identified where your bottlenecks are, you will then be able to put strategies in place to ensure that your bottleneck is running at maximum efficiency. Quality checking parts before they enter the bottleneck, reducing the load on the bottleneck, and increasing the capacity of the bottleneck are all ways to exploit the bottleneck.
Once you have identified and exploited your bottleneck, you will often find that the bottleneck moves to another area of your production and you need to go through this process again to exploit that bottleneck.
Reduce Downtime
Reducing unplanned downtime is key to improving production output. Unplanned downtime is usually the result of one of two reasons; machine break downs, or staff breaks.
Machine break downs can be minimised by holding regular preventative maintenance sessions on your machinery. Whilst it may appear inefficient to regularly shut down your production for maintenance, if it is done in a planned manner, you will find there’s less lost production output from this than there would be from unplanned breakdowns.
Staff breaks are the other reason for downtime in a production process. There are two different approaches to minimising downtime from staff breaks, and you will need to decide which method works best for your production process. One method is to ensure that your staff take staggered breaks so that the production process can continue to run constantly. The other method is to ensure that your staff all take their breaks at the same time, for the same length of time. This means that your production process will stop for a set amount of time each day, but it will be predictable and controlled, and you know it will be running efficiently in between these break times.
Stay Organized
Disorganisation can result in many lost man-hours and wasted production time. Ensuring that your manufacturing plant is clearly organised and kept tidy will save many hours of lost production. Make sure every tool, part, or product has a clearly marked place where it should live.
When organising each working area think about how and when the tools or parts are going to be used, and ensure that they are stored in the most efficient place for what they are going to be used for. Think about your manufacturing floor as a whole, is everything in the most efficient place? Is there anything that could be easily and simply moved to improve efficiencies and thus improve production output?
Reduce The Walking
Reducing the walking that your production staff have to do is a basic lean principle of saving wasted time/motion. However, there is a further significant benefit to reducing walking that is not often talked about. When staff have to walk off your production process to get something, they will often be passing other staff on the way, and will often stop for a quick hello or a chat. Before you know it, 5 wasted minutes have passed. If one member of your production process is having a 5 minute chat every 50 minutes, this is reducing your productivity by 10%!
Look at your production process and see what walking is having to be done by your staff. Find ways to reduce the walking or minimise it as far as possible and you will start to see an increase in productivity.
Daily Production Line Audit
Take a daily walk around your production area, and make sure you do this at a different time each day. Before you go for your walk around, take off your managers ‘hat’ and put on your improvements, problem finder ‘hat’; take a view of your production as a whole with no preconceptions. Talk to your staff, find out what’s gone well for them so far today and what hasn’t.
As you do these daily walk rounds you will begin to build up a picture of what is actually going on in the production process and you will start to see where the inefficiencies are and where improvements could be made. It may even make you start to question some of the processes and whether they are necessary of if there could be a better way of doing them.
Identify Wastage
Identifying wastage in your process is key to streamlining and improving your production output. The eight key wastes in lean manufacturing are;
- Overproduction
- Waiting (time on hand)
- Unnecessary transport or conveyance
- Overprocessing or incorrect processing
- Excess inventory
- Motion
- Defects
- Unused employee genius
Analyse your production processes, which of these wastes do you have, how can you minimise or eliminate them?
Get New Machinery At No Net Cost To Your Bottom Line
Having worked through all of the above you may find that you need to introduce some new machinery to improve your production process. If this is the case, you need to look for a company that offers finance deals on the purchase of new machinery such as palletisers, bespoke machinery, vision systems, etc. With the right finance deal, you will find that you will be getting more ROI from the new machinery than the repayments on the finance deal. What’s more, with a finance deal there is no need for an initial capital outlay as repayments can be spread over a longer period of time, enabling you to realise the benefit of the new machinery whilst making capital repayments. Try our automation project payback calculator as this calculates ROI as well as showing finance deal options and costs. Download the calculator here.
If you would like to discuss any aspect of this article in more detail then feel free to contact us on 01223 499488.
Watch automation videos…
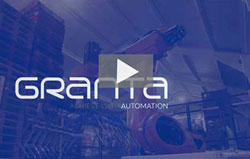