In recent years, the introduction of cobot palletisers has greatly enhanced manufacturing industries by offering an efficient and flexible solution for handling repetitive palletising tasks. These collaborative robots (or “cobots”) can work alongside humans, optimising productivity while reducing the risks of injuries associated with manual labour. But what exactly are cobot palletisers, and what are the advantages and disadvantages of integrating them into your business? Let’s look at the details.
What Is a Cobot Palletiser?
A cobot palletiser is a type of collaborative robot (or “cobot”) designed to automate the process of stacking various products — such as boxes, bags, or other items — onto pallets in a warehouse or production environment. Unlike traditional robotic systems that often require dedicated safety enclosures and complex programming, cobot palletisers are specifically designed to safely work in close proximity to humans, providing a flexible and user-friendly solution for automating repetitive tasks. If they are installed with integrated safety and guarding, then they can also run at industrial palletising speeds, making them a very fast efficient combined solution. They are ideal for businesses that have limited space available and are seeking to improve their operations productivity.
Cobot palletisers typically use a vacuum or paddle gripper to pick up products from a conveyor belt or another feeding mechanism, and they stack these products according to a pre-selected pattern on a pallet. They are typically designed for ease of use, featuring intuitive programming interfaces that allow operators to configure different palletising patterns or adjust parameters without specialised training. Integration into existing production environments is straightforward, thanks to their plug-and-play design, which minimises setup time and eliminates the need for extensive programming expertise.
The Pros of Cobot Palletisers
1. Increased Productivity: Cobot palletisers can operate continuously, handling repetitive tasks without the need for breaks, rest, or shifts. Unlike human workers, they do not experience fatigue, which allows them to sustain high levels of output throughout their operation. This consistent, uninterrupted workflow can significantly boost production rates compared to manual palletising. Additionally, cobots can work around the clock, maintaining efficiency during extended production runs, which ultimately contributes to reduced cycle times and higher overall throughput.
2. Enhanced Safety: One of the primary benefits of cobot palletisers is their built-in safety features, designed for collaborative work environments. These robots are equipped with advanced force and proximity sensors that monitor the surrounding area and detect the presence of humans. If a worker approaches too closely, the cobot will automatically slow down, pause, or stop entirely to prevent collisions or injuries. This is a stark contrast to traditional industrial robots, which typically require safety areas or barriers to protect workers. The cobot’s ability to safely operate alongside human workers without extensive safety precautions makes them ideal for shared workspaces, reducing the risk of accidents and enhancing overall workplace safety. Cobot’s can also be installed with area scanners or guarding, which allows them to work at full industrial speeds, simply slowing to cobot speed if the safety is breached, and returning to industrial speeds once it is reset.
3. Flexibility and Adaptability: Cobots are highly versatile and can be easily reprogrammed to accommodate various tasks, products, and palletising patterns. This flexibility makes them invaluable in environments where production needs frequently change. For example, if a company introduces a new product or changes the packaging design, a cobot palletiser that has easy programming software can be swiftly reconfigured to handle the updated palletising process. This adaptability not only reduces the time and cost of reprogramming for new product lines but also helps businesses remain agile and responsive to shifting market demands. As production needs evolve, cobot palletisers can continue to provide efficient, customised solutions with minimal downtime.
4. Improved Ergonomics for Workers: Cobot palletisers are designed to take over repetitive and physically demanding tasks that are traditionally done by human workers. These tasks, such as lifting heavy items or repeatedly bending and twisting to stack products, can lead to musculoskeletal disorders and repetitive strain injuries over time. By automating the palletising process, cobots help reduce the physical strain on workers, creating a healthier and more ergonomic work environment. Human operators are then free to focus on more complex, value-added activities, such as quality control, system monitoring, or process optimisation, improving overall job satisfaction and productivity.
5. Space Efficiency: Cobots are typically more compact and flexible in their installation compared to large industrial robots, which often require dedicated safety zones and substantial floor space. Cobot palletisers can be easily integrated into existing production lines without the need for extensive modifications or additional infrastructure, making them ideal for companies with limited workspace. Their small footprint allows manufacturers to maximise their facility layout and maintain operational efficiency, even in smaller factories or production areas. This space-saving aspect is particularly beneficial for businesses that are looking to enhance automation without expanding their physical plant.
The Cons of Cobot Palletisers
1. Speed Limitations in Collaborative Mode: Cobot palletisers, when operated in collaborative mode, must adhere to strict safety regulations that limit their speed to ensure they can safely interact with humans in shared workspaces. This often means that cobots run significantly slower than their full capacity in collaborative mode, which can affect the overall efficiency and commercial viability of the system in high-speed production environments. To overcome this, most installations require the implementation of additional safety measures, such as physical guarding or area safety scanners. These features allow cobot palletisers to operate at higher speeds while maintaining compliance with CE and UKCA safety requirements. However, the need for extra safety infrastructure adds complexity and cost, potentially reducing the simplicity and flexibility that cobots are known for.
2. High Initial Investment: While cobots are often marketed as a more affordable alternative to traditional robots, the initial investment for implementing a cobot palletising system can still be substantial. Businesses must not only account for the cost of the cobot itself but also for the integration, safety measures, and any necessary modifications to existing infrastructure. Additionally, custom programming or system integration may be required to ensure that the cobot functions seamlessly within the production line, which can increase the overall cost. For small and medium-sized enterprises (SMEs), these upfront expenses may represent a significant financial hurdle, making it challenging to justify the investment, particularly if the expected return on investment (ROI) is not immediate.
3. Limited Payload and Speed: Cobot palletisers generally have lower payload capacities and slower operational speeds compared to traditional industrial robots. While they are well-suited for light- to medium-weight tasks, their ability to handle heavy loads is often limited. In applications where larger products or higher throughput are required, cobots may struggle to keep pace with the demands of production. For example an industrial robot with 120kg capacity can lift a whole row, group or layer of products during palletising significantly increasing production speeds. Although a cobot can theoretically do the practical reality is that the payload is quickly exceeded when picking and placing multiple products at once. However for lightweight products the Cobot palletiser can work perfectly well and just as fast. As a result, businesses need to carefully evaluate whether the specific requirements of their palletising tasks align with the capabilities of cobot systems.
4. Complex Programming and Technical Expertise: Although cobot manufacturers have made significant strides in developing user-friendly interfaces, programming and configuring a cobot palletiser, some systems still require a certain level of technical knowledge and expertise. It is essential to choose a cobot palletiser system that has easy programming software with automatic stack pattern generation, otherwise product changeovers can be costly and time consuming.
5. Integration Challenges: Incorporating a cobot palletiser into an existing production line can be a complex process, especially if the current infrastructure or control systems are not compatible with the new automation technology. Successful integration requires the cobot to work in coordination with other equipment, such as conveyor belts, sensors, or packaging machines. Achieving this level of synchronisation often involves additional engineering and customisation, which can be time-consuming and costly. Without careful planning, these integration challenges can result in significant downtime or inefficiencies during the transition to automation.
6. Human Dependency and Operational Inefficiencies: Despite their name, collaborative robots (cobots) still rely on human operators for various tasks such as supplying materials. While the cobot can handle the palletising process, it is not entirely autonomous. If human workers are unavailable or slow to respond, the cobot may experience downtime, waiting for pallets to be changed over, which can introduce operational inefficiencies.
From space-saving design to cost-efficiency and ease of programming, cobot palletisers are an attractive option for businesses looking to automate without the hefty costs and complexity associated with traditional robots. However, it is important to carefully consider potential limitations such as payload capacity, speed, and programming complexity before deciding if a cobot palletiser is the right fit for your operations.
If you would like to know more about the Granta Cobot Palletiser, then please do get in touch on 01223 499488 or contact us at helpline@granta-automation.co.uk. We will also be very happy to arrange a free demonstration at our site.
Watch automation videos…
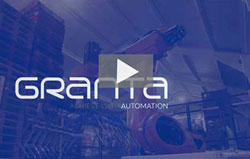
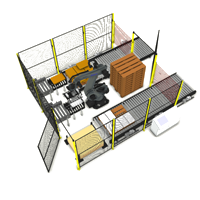
Bag Palletiser
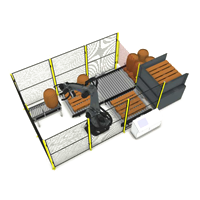
Barrel Palletiser
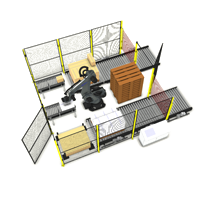
Box Palletiser
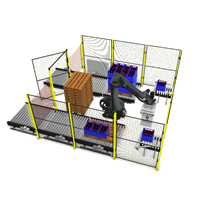
Crate Palletiser
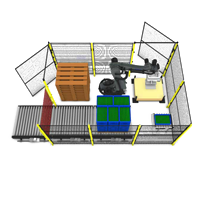
Tray Palletiser