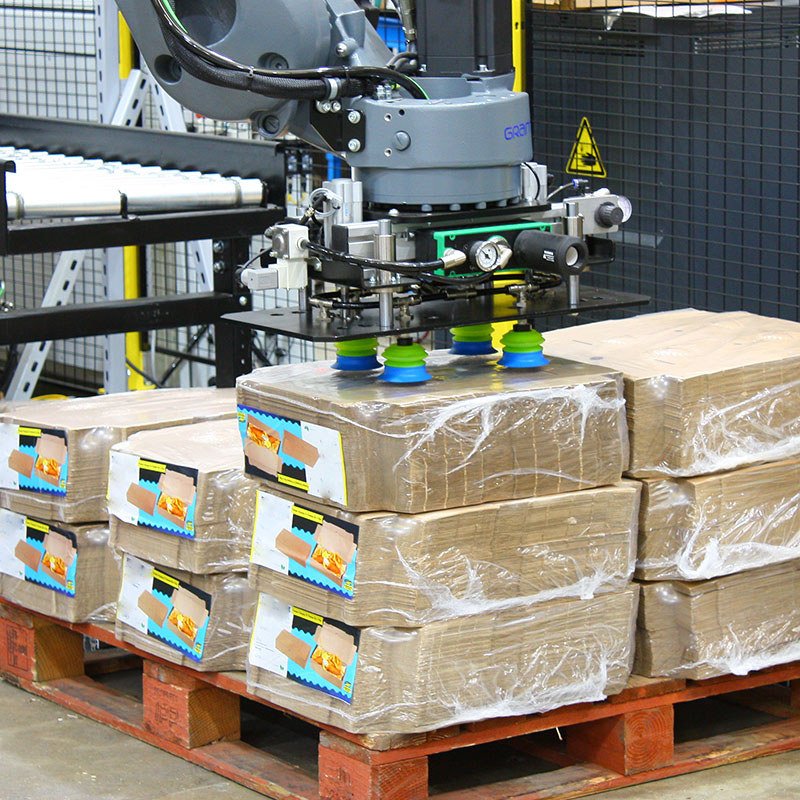
Palletising, the process of stacking products onto pallets for storage or shipping, is a crucial aspect of many industries, including manufacturing, logistics, and retail. However, manual palletising can be labour-intensive, time-consuming, and prone to errors, leading to increased labour costs and reduced efficiency. Reducing these costs while maintaining or improving productivity is essential for businesses to stay competitive. Here are several strategies to achieve this:
1. Implement Automated Palletising Systems
Robotic Palletisers: Investing in robotic palletisers can significantly reduce labour costs. These machines can handle repetitive tasks with high accuracy and consistency, reducing the need for manual labour. Robotic arms equipped with advanced grippers can handle various product shapes and sizes, improving overall efficiency. Additionally, robotic palletisers can operate continuously without fatigue, leading to increased throughput and reliability.
Automated Guided Vehicles (AGVs) and Autonomous Mobile Robots (AMRs): AGVs/AMRs can transport pallets within the facility, reducing the need for human-operated forklifts. They can be programmed to follow specific paths, ensuring timely and efficient pallet movement. This not only reduces labour costs but also enhances safety by minimising human interaction with heavy machinery.
2. Enhance Workflow Efficiency
Optimise Layout: Analyse the layout of your palletising area to minimise unnecessary movement and handling. Ensure that products, pallets, and equipment are strategically placed to streamline the palletising process. A well-designed layout can significantly reduce the time and effort required for palletising, leading to lower labour costs and increased productivity.
Lean Manufacturing Principles: Implement lean manufacturing principles to eliminate waste and improve efficiency. Techniques such as 5S (Sort, Set in order, Shine, Standardise, Sustain) can help organise the workspace and reduce time spent on non-value-added activities. Lean practices can also uncover hidden inefficiencies and opportunities for improvement.
Standard Operating Procedures (SOPs): Develop and enforce SOPs for palletising tasks. Clear guidelines and training can help workers perform their tasks more efficiently and consistently. SOPs also ensure that best practices are followed, reducing errors and enhancing overall productivity.
3. Invest in Ergonomic Solutions
Ergonomic Tools: Provide workers with ergonomic tools such as lift-assist devices, pallet jacks, and adjustable height workstations. These tools can reduce physical strain and fatigue, improving productivity and reducing the risk of injuries. Ergonomic solutions not only enhance worker comfort but also lead to fewer work-related injuries and associated costs.
Training Programs: Conduct regular training programs on proper lifting techniques and the use of ergonomic equipment. Educated workers are less likely to experience work-related injuries, leading to fewer lost workdays and lower labour costs. Continuous education on ergonomics can foster a culture of safety and efficiency.
4. Utilise Data and Analytics
Performance Monitoring: Implement systems to monitor and analyse the performance of your palletising operations. Data on cycle times, error rates, and downtime can help identify bottlenecks and areas for improvement. Performance data can enable quick decision-making and adjustments to maintain optimal productivity.
Preventative Maintenance: Regular preventative maintenance can reduce unexpected downtime and maintain smooth operations. Proactive maintenance ensures that machinery operates efficiently, extending its lifespan and reducing long-term costs.
5. Adopt Flexible Staffing Strategies
Cross-Training Employees: Cross-train employees to perform palletising. This flexibility allows you to allocate labour more efficiently based on workload demands. Cross-trained employees can adapt to different roles, reducing the need for additional hires and ensuring operational continuity.
Temporary Staffing: During peak periods, consider hiring temporary workers to handle increased demand. This approach can help manage labour costs by scaling the workforce up or down as needed. Temporary staffing provides the agility to respond to market fluctuations without long-term labour commitments.
6. Leverage Technology for Process Improvement
Warehouse Management Systems (WMS): Implement a WMS to optimise inventory management and order fulfilment processes. A WMS can streamline the palletising process by ensuring that the right products are available at the right time. This reduces delays and improves the efficiency of the entire supply chain.
Palletising Software: Use specialised palletising software to design optimal pallet patterns and configurations. Efficient stacking patterns can maximise space utilization and reduce the number of pallets needed, leading to cost savings. Palletising software can also simulate different scenarios to find the most efficient loading strategies.
By implementing these strategies, businesses can improve productivity, enhance worker safety, and ultimately reduce labour costs, leading to a more efficient and competitive operation. Investing in modern palletising solutions not only cuts costs but also positions businesses for long-term success in a rapidly evolving marketplace.
If you would like to know more about the Granta palletising systems, then please do get in touch on 01223 499488 or contact us at helpline@granta-automation.co.uk. We will be very happy to help.