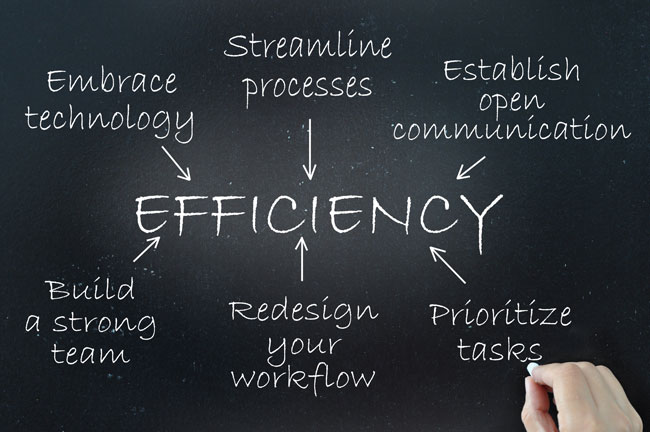
Improving throughput during peak production periods is crucial for maintaining efficiency, meeting customer demand, and maximising profitability. This often requires a strategic blend of process optimisation, automated technology, workforce management, and effective coordination. Here are some simple strategies that can be implemented to enhance throughput:
Process Optimisation
- Streamline Workflows:
- Identify and Eliminate Bottlenecks: Conduct a thorough analysis of your production processes to pinpoint bottlenecks. Implement solutions to alleviate these constraints and smooth the flow of operations.
- Standardise Procedures: Develop and enforce standardised operating procedures (SOPs) to ensure consistency and efficiency across all production stages. SOPs help in reducing variability and increasing reliability.
- Lean Manufacturing:
- Minimise Waste: Adopt lean manufacturing principles to eliminate waste in all forms; whether it’s excess inventory, unnecessary movement, or inefficient processes.
- Just-In-Time Production: Implement just-in-time (JIT) production techniques to reduce inventory costs and enhance responsiveness to customer demand. This approach ensures that materials arrive only when needed, reducing storage requirements.
- Kaizen and Continuous Improvement:
- Foster a culture of continuous improvement (Kaizen) where employees are encouraged to suggest and implement small, incremental changes. These small changes accumulate to significant improvements over time.
Workforce Management
- Cross-Training Employees:
- Enhance Flexibility: Cross-train employees to perform multiple roles, increasing the flexibility of your workforce. This allows for quick reallocation of labour to where it is most needed during peak periods.
- Incentive Programs:
- Motivate Performance: Implement incentive programs that reward employees for high performance and efficiency. Recognition and rewards can drive employees to maintain peak productivity.
- Flexible Scheduling:
- Adapt to Demand: Utilise flexible work schedules to ensure that labour is available during peak demand times. This might include staggered shifts, part-time work, or overtime as necessary.
Technology and Automation
- Automation
- Reduce Human Error and Increase Speed: Implement automation in repetitive and time-consuming tasks. Automated systems can operate continuously with high precision, reducing errors and increasing throughput.
- Automated Palletising: Integrate automated palletising systems to handle the stacking and organising of products onto pallets. This reduces manual labour, speeds up the packaging process, and ensures consistent pallet quality.
- Advanced Manufacturing Technologies:
- Utilise Cutting-Edge Tools: Where possible, invest in advanced manufacturing technologies such as 3D printing, robotics, and CNC machines. These tools can significantly enhance production speed and accuracy.
- ERP Systems:
- Integrate Operations: Deploy Enterprise Resource Planning (ERP) systems to integrate production planning, scheduling, and inventory management. An ERP system provides real-time data and analytics, facilitating better decision-making.
Supply Chain and Inventory Management
- Supply Chain Optimisation:
- Ensure Timely Deliveries: Improve coordination with suppliers to ensure timely delivery of raw materials and components. Establish strong supplier relationships to secure priority during high-demand periods.
- Resilient Supply Chains: Develop a resilient supply chain that can quickly adapt to changes in demand and supply conditions.
- Inventory Management:
- Smart Techniques: Implement inventory management techniques like ABC analysis to prioritise high-value items. Use methods such as safety stock and buffer inventory to handle unexpected spikes in demand without disrupting production.
Facility and Equipment Management
- Preventive Maintenance:
- Avoid Downtime: Schedule regular preventive maintenance to prevent unexpected equipment failures. Well-maintained machinery operates more efficiently and reduces downtime during critical periods.
- Capacity Expansion:
- Increase Production Capacity: Consider temporary or permanent capacity expansion by adding additional shifts, purchasing new machinery, or outsourcing parts of the production process.
Data and Analytics
- Real-Time Monitoring:
- Quick Issue Resolution: Implement real-time monitoring systems to track key production metrics. This enables quick identification and resolution of issues, minimising disruption.
- Data Analytics:
- Predictive Insights: Leverage data analytics to accurately forecast demand and plan production schedules. Data-driven insights can optimise resource allocation and improve overall efficiency.
Quality Control
- Enhanced Quality Control:
- First-Time Right: Implement stringent quality control measures to ensure products meet quality standards on the first pass. Reducing rework and defects directly improves throughput.
Communication and Coordination
- Effective Communication:
- Keep Everyone Aligned: Improve communication channels within the production team and across departments. Clear and efficient communication ensures everyone is informed and aligned with production goals.
- Integrated Planning:
- Collaborative Approach: Coordinate planning efforts across departments such as sales, marketing, and production. Integrated planning ensures that production aligns with market demand and organisational goals.
By implementing some, or all of these comprehensive strategies, you can significantly enhance throughput during peak production periods. This leads to better operational efficiency, reduced costs, and improved customer satisfaction, ultimately driving higher profitability and competitive advantage. Automated palletising, in particular, can be a game-changer by reducing manual labour, increasing speed, and ensuring consistency in product handling, further boosting overall throughput.
Find out more…
- How Do You Keep Production Running During Pallet Change Overs When Using An Automated Palletising System?
- Can a Palletiser Stack Mixed Products Like Boxes and Open Top Trays with the Same Gripper?
- Can A Palletiser Palletise Off Multiple Lines With One Robot?
- What are the Pros and Cons of Modular, Compact and Cobot Palletisers?
- Palletiser vs Smart Car