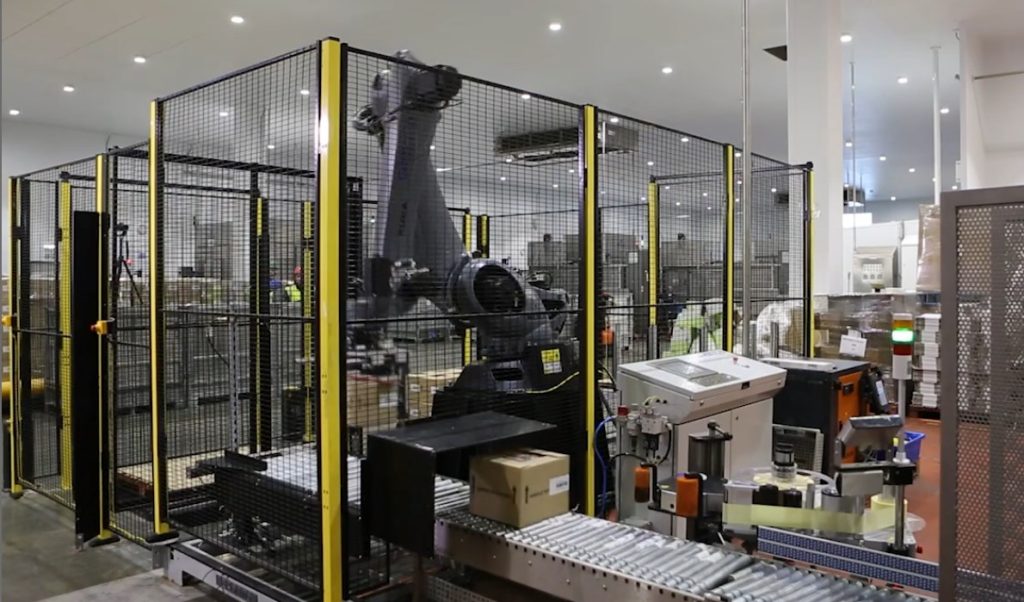
As the pet foods industry continues to evolve, the need for efficient and reliable palletising solutions has never been more crucial. From handling a variety of packaging types to ensuring speed and precision, here’s a comprehensive guide to choosing the right palletiser for your operations.
Types of Palletisers
There are many different palletising systems on the market, each suited to different processes and product types. Below is an overview of some of the more common types:
- Robotic Palletisers
Robotic palletisers are highly adaptable, capable of handling different packaging formats such as boxes, bags, cans, and pouches. They are ideal for a wide range of applications, and are capable of palletising single items, rows, or whole layers.
Palletiser with easy programming software can be quickly reprogrammed by production staff for different box sizes and configurations; making them highly adaptable. Their programming flexibility allows for easy adjustments to stacking patterns and configurations.
- Layer Formers
Layer former palletisers are best suited to applications with consistent product shapes and sizes; palletising products in layers at very high speeds. New product setups and configurations typically require a programmer. - Collaborative Palletisers
Collaborative palletisers are best suited for applications where products can be vacuum picked from the top. They are not suitable for underneath or bag gripping due to their low payload capabilities.
Despite being called collaborative, these systems typically need guarding or laser area scanning to comply with safety standards. This additional safety also allows the cobot to run at industrial speeds until the safety is compromised by a person entering the cell, at which point it will continue to run but at collaborative speeds.
Each system type has its unique advantages, and the choice depends on your specific palletising needs and production requirements.
Product Handling Capabilities
Palletisers in the pet foods industry need to accommodate various packaging types. Almost any type of product can be automatically palletised by using the appropriate gripper for picking and placing items onto pallets. Additionally, slip sheets can be automatically inserted between layers, and completed pallets can be shrink-wrapped automatically. Common products suitable for automatic palletising include:
- Boxes/Cartons/Display Boxes
- Bags/Sacks
- Open-Top Boxes
- Trays/Bale Arm Crates
- Bottles
- Cans
- Pouches
- Barrels/Drums
- Collation/Transit Trays
Palletiser Gripper Types
The type of gripper required for palletising depends on the specific product, with many grippers also capable of handling slip sheets and pallets. Here’s a detailed look at different grippers and their applications:
- Foam Vacuum Gripper: A foam vacuum gripper is best suited for flat-topped products like boxes, display boxes, cartons, and certain types of cans. This gripper utilises vacuum suction to securely lift and place items onto pallets.
- Vacuum Row Gripper: A vacuum row gripper increases palletising speeds by picking and placing multiple items simultaneously. It is commonly used for boxes, cartons, and some cans, optimising throughput in high-volume operations.
- Bag Gripper: For products like sacks and bags that cannot be effectively handled with vacuum suction, a bag gripper is typically used. This gripper features positioning pins, lifting pins, and a center clamp to provide stable support during handling.
- Underneath Gripper: The underneath gripper has tines that go underneath the product and a clamping arm that clamps onto the top of the product whilst it is being lifted. This design is suitable for open-top plastic or cardboard crates, weak boxes, shrink-wrapped items, and products in transit trays.
- Parallel Gripper: Distinguished by their two side plates that close in parallel, they are best suited to regular-shaped boxes that do not lend themselves to vacuum gripping.
- Barrel Gripper: Barrel grippers are specifically designed with curved arms to clamp around barrels or drums securely, offering a reliable solution for items that cannot be lifted using vacuum technology.
- Bespoke Gripper: In cases where standard grippers do not meet the requirements, bespoke grippers are custom-made. These are tailored for irregularly shaped or oversized items, such as large 25L bottles or products requiring specific lifting methods, like those with handles.
Watch some videos showing some of the different gripper types and products being palletised here.
Key Considerations
There are many different things that need to be considered when specifying a palletiser to ensure that is will meet your current needs and potential future requirements. Some of the key things to consider include:
- Product Variety: Ensure the chosen palletiser can handle the full range of packaging formats used in your operations. Pet foods come in various packaging formats – bags, cans, pouches. Palletisers need to handle this diversity.
- Speed and Efficiency: Match the palletiser’s speed with production demands to avoid bottlenecks and maximize throughput.
- Automation Integration: Seamless integration with existing automation systems is crucial for efficient operation and control.
- Scalability: Select a palletising system that can scale with your production growth, accommodating increases in volume and product types without requiring significant additional capital outlay.
This is just a brief overview of the many different things that need to be considered when specifying a palletiser system, and they are all explained in more detail here. There is also a downloadable Palletiser URS document available for you to download and modify to suit your specification, to ensure that you have covered everything when specifying your palletiser. It can be downloaded here.
If you would like to discuss your specific palletising application, feel free to contact us on 01223 499488 or helpline@granta-automation.co.uk and we will be very happy to help.
Find out more…
- The Role of Automated Palletising in Reducing RSI
- Compact palletising systems can be leased for as little as £3.96 per hour!
- Ways to Improve Throughput During Peak Production Periods
- How Do You Keep Production Running During Pallet Change Overs When Using An Automated Palletising System?
- Can a Palletiser Stack Mixed Products Like Boxes and Open Top Trays with the Same Gripper?
Warning: Undefined variable $aria_req in /var/www/granta-automation.co.uk/news/wp-content/themes/twentyten/comments.php on line 81
Warning: Undefined variable $aria_req in /var/www/granta-automation.co.uk/news/wp-content/themes/twentyten/comments.php on line 86