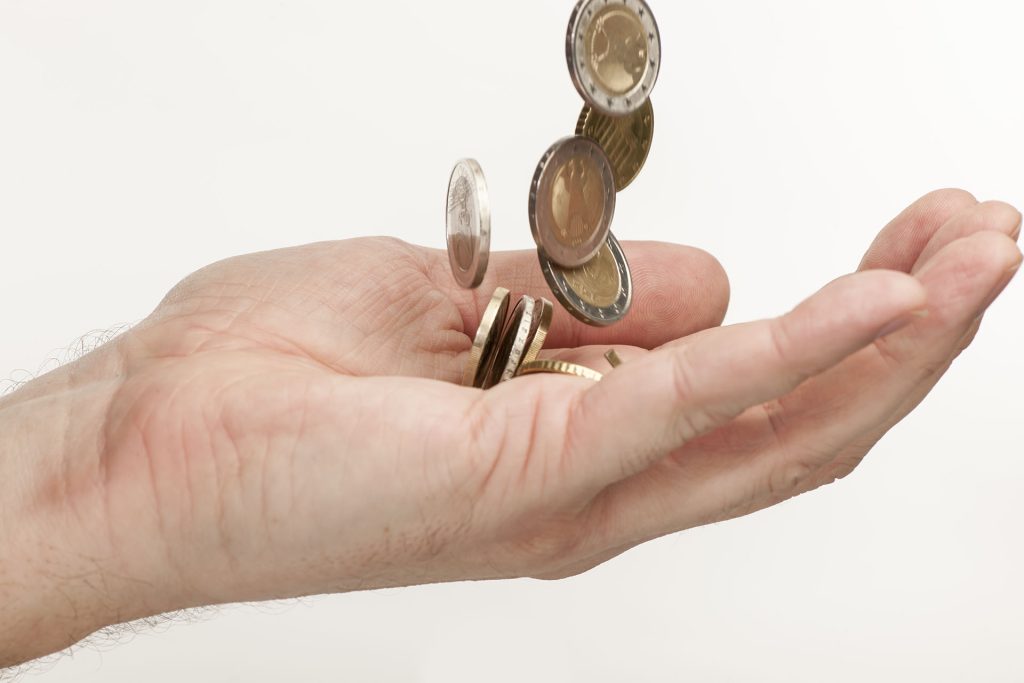
In the manufacturing industry, managing costs effectively is paramount to sustaining profitability and competitiveness. Managers are continually challenged to find ways to reduce costs without sacrificing quality while also ensuring that investments yield the highest possible returns. This article looks into two critical aspects of cost management: cost reduction strategies and ROI optimisation.
Cost Reduction Strategies: Identifying Ways to Reduce Costs Without Compromising Quality
Reducing costs while maintaining, or even improving, product quality requires a strategic and multifaceted approach. Here are several proven strategies that can be implemented:
- Lean Manufacturing:
- Eliminate Waste: Identify and eliminate waste in all forms—overproduction, waiting times, excess inventory, unnecessary motion, defects, over-processing, and underutilised talent. Techniques such as value stream mapping can help pinpoint inefficiencies, streamline operations, and enhance productivity.
- Continuous Improvement (Kaizen): Foster a culture of continuous improvement where employees at all levels are encouraged to suggest and implement incremental improvements. This approach not only leads to significant cost savings but also boosts employee engagement and innovation.
- Supply Chain Optimisation:
- Supplier Partnerships: Develop strong relationships with suppliers to negotiate better pricing, improve supply chain reliability, and reduce lead times. Collaborative planning, forecasting, and replenishment (CPFR) can enhance inventory management and reduce costs associated with stockouts or excess inventory.
- Bulk Purchasing: Take advantage of bulk purchasing discounts and consolidate orders to reduce shipping and handling costs. Additionally, implementing vendor-managed inventory (VMI) systems can further streamline the supply chain.
- Technology and Automation:
- Invest in Automation: Automate repetitive and labour-intensive tasks to reduce labour costs, increase production speed, and improve precision. Robotics, AI, and IoT technologies can significantly enhance operational efficiency, reduce errors, and minimize waste.
- Adopt Advanced Manufacturing Technologies: Implement technologies such as 3D printing, CNC machining, and advanced robotics to streamline production processes and reduce material waste. These technologies can also enable more flexible and customized manufacturing capabilities.
- Energy Efficiency:
- Conduct Energy Audits: Regularly assess energy use and identify areas where efficiency can be improved. Upgrading to energy-efficient machinery, optimising facility layouts, and implementing energy management systems can result in substantial energy savings and reduced operational costs.
- Utilise Renewable Energy: Invest in renewable energy sources such as solar or wind power to reduce long-term energy costs and enhance sustainability. Government incentives and rebates can also offset some of the initial investment costs.
- Workforce Training and Development:
- Employee Training: Invest in comprehensive training programs to enhance employee skills, productivity, and safety. Well-trained employees can operate machinery more efficiently, reduce error rates, and contribute to process improvements.
- Cross-Training: Cross-train employees to perform multiple roles. This approach reduces downtime caused by absences, improves workforce flexibility, and ensures that critical operations can continue seamlessly.
- Effective Inventory Management:
- Just-in-Time (JIT) Inventory: Implement JIT inventory systems to reduce inventory holding costs and minimise waste. This approach aligns inventory levels closely with production schedules and demand forecasts, reducing the risk of overproduction and obsolescence.
- Inventory Analysis: Use ABC analysis to categorize inventory based on importance and turnover rates, allowing for better inventory control and reduced carrying costs. Additionally, implementing automated inventory management systems can provide real-time visibility and optimisation.
ROI Optimisation: Ensuring Investments Yield the Highest Possible Returns
Maximising the return on investment (ROI) is crucial for justifying capital expenditures and ensuring long-term financial health. Here’s some strategies that can be implemented to optimise ROI:
- Thorough Feasibility Studies:
- Conduct comprehensive feasibility studies before making any investment. Analyse market trends, competitive landscape, technological advancements, and financial projections to ensure the investment aligns with strategic objectives and has a high likelihood of success. Engaging cross-functional teams in these studies can provide diverse insights and improve decision-making.
- Clear Performance Metrics:
- Establish clear performance metrics and key performance indicators (KPIs) to measure the success of investments. Metrics such as payback period, net present value (NPV), internal rate of return (IRR), and total cost of ownership (TCO) are essential for evaluating investment performance. Regular monitoring and reporting on these metrics ensure transparency and accountability.
- Project Prioritisation:
- Prioritise projects based on their potential ROI and strategic importance. Focus on initiatives that align with long-term goals, enhance competitive advantage, and offer the most significant financial benefits. This strategic prioritisation ensures that limited resources are allocated to the most impactful projects, maximising overall returns.
- Continuous Monitoring and Improvement:
- Implement a system for continuous monitoring of investments. Regularly review performance data to identify underperforming assets and make necessary adjustments. This proactive approach ensures investments remain on track to deliver expected returns and allows for agile responses to changing market conditions.
- Risk Management:
- Develop a robust risk management strategy to mitigate potential risks associated with investments. Conduct risk assessments, scenario planning, and sensitivity analysis to prepare for uncertainties and minimise potential losses. Establishing contingency plans and risk mitigation measures can safeguard investments and ensure smoother project execution.
- Post-Investment Analysis:
- Conduct post-investment reviews to evaluate the actual performance of investments against initial projections. Identify lessons learned and apply them to future investment decisions. This feedback loop helps refine investment strategies, improve future outcomes, and build a knowledge base for better decision-making.
In a constantly evolving industry, staying agile and forward-thinking is key. Embracing these cost management strategies will enable you to navigate challenges, capitalise on opportunities, and secure a competitive edge in the market. By fostering a culture of continuous improvement, leveraging advanced technologies, and prioritising strategic investments, you can drive sustainable success and growth in an increasingly competitive landscape.
If you would like to know more about the Granta palletising systems or AMR/AGV systems, then please do get in touch on 01223 499488 or contact us at helpline@granta-automation.co.uk. We will be very happy to help.
Find out more…
- Ways To Speed Up The Palletising Process In Production
- How To Automate Cross Palletising and Depalletising from UK to Euro Pallets
- How Cycle Time Reduction Improves Operational Efficiency
- Autonomous Mobile Robot (AMR) Pallet Stations, Charging Stations, and Conveyor Stations
- Mastering Budget Planning: Advanced Methods for Planning and Allocating Capital Budgets in Manufacturing
Warning: Undefined variable $aria_req in /var/www/granta-automation.co.uk/news/wp-content/themes/twentyten/comments.php on line 81
Warning: Undefined variable $aria_req in /var/www/granta-automation.co.uk/news/wp-content/themes/twentyten/comments.php on line 86