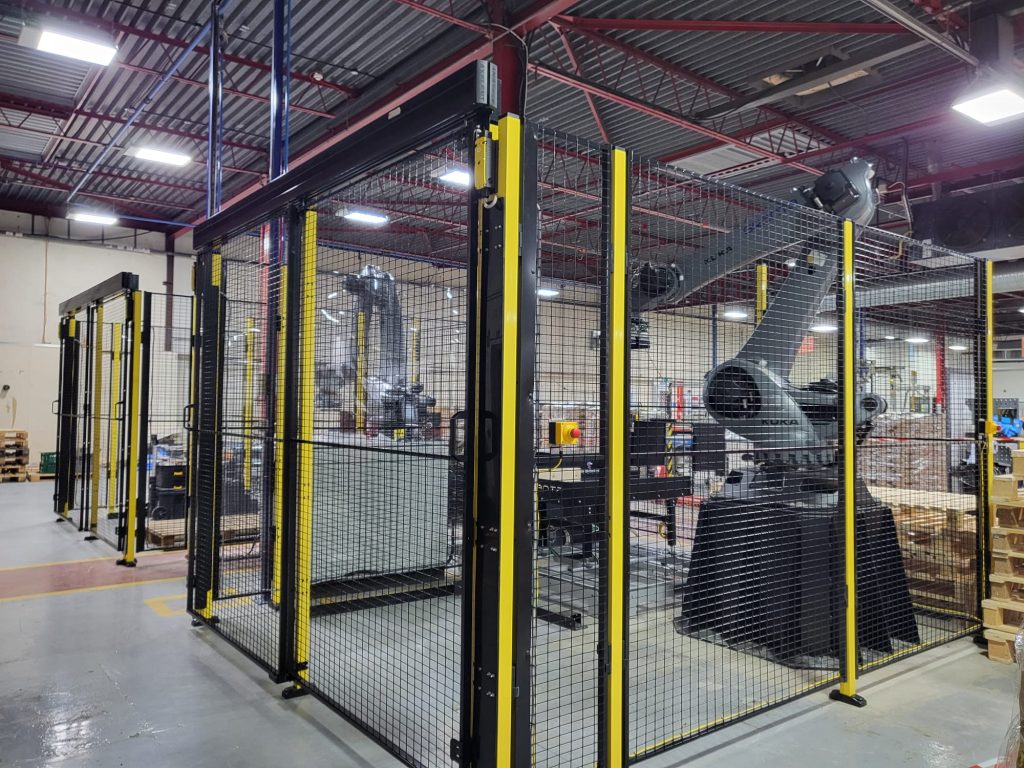
Optimising the palletising process in production is crucial for enhancing overall efficiency, reducing operational costs, and maintaining a smooth workflow. In today’s competitive manufacturing environment, speeding up palletising not only boosts productivity but also improves product handling and distribution. This article outlines a range of specific strategies and technologies designed to significantly accelerate the palletising process, from advanced equipment and software solutions to ergonomic enhancements and lean manufacturing techniques. By implementing these targeted approaches, manufacturers can achieve faster, more reliable palletising operations, ultimately contributing to a more efficient and profitable production line.
1. Palletising Equipment
- Robotic Palletisers: Invest in a robotic palletiser suitable for your production volumes and product types. Even entry-level models can handle multiple SKUs and configurations if they have easy programming software. These robots can work continuously without fatigue, maintaining high precision and consistency in palletising tasks, which significantly enhances overall productivity.
- Layer Forming Palletisers: If your production is high speed, then consider using layer forming palletisers that can form and place entire layers of products on a pallet in one motion. This approach drastically reduces the time needed compared to placing individual items and is particularly effective for uniform product sizes and shapes.
2. Conveyor Integration
- Infeed Conveyors: Implement high-speed infeed conveyors to deliver products swiftly to the palletising area. Ensure that the conveyor system is fully synchronised with the palletiser to prevent bottlenecks. The use of conveyors minimises manual handling, reducing labour costs and speeding up the process.
- Accumulation Conveyors: Utilise accumulation/buffering conveyors to create a buffer of products ready for palletising. This ensures a steady and continuous supply, allowing the palletiser to operate at maximum efficiency without waiting for the next batch of products.
3. Pallet Pattern Optimization
- Pattern Forming Software: Utilise advanced pallet pattern optimisation software to design the most efficient loading patterns. This will be included as standard on a good palletising system and it will automatically calculate optimal stacking patterns, ensuring maximum pallet stability and efficient use of space. This reduces the number of cycles needed and minimises the risk of pallet collapse during transportation.
- Easy Programming Software: If you are palletising multiple sizes of product off the production line, it is essential to ensure that the system has easy programming software. This will enable staff to quickly reprogram the palletiser for new product sizes. This adaptability can significantly improve throughput by reducing the need to wait for an experienced robot programmer to set up a new stack pattern.
4. End-of-Arm Tooling (EOAT) Enhancements
- Multi-Pick EOAT: Equip robotic arms with end-of-arm tooling capable of picking up multiple items simultaneously – such as row gripping or layer forming. This feature reduces the number of cycles required to complete a pallet, thereby speeding up the entire palletising process.
- Adjustable Grippers: Invest in EOAT with adjustable grippers to handle a variety of product shapes and sizes without the need for manual changeovers. This versatility is crucial for operations handling multiple SKUs, as it allows for quick transitions between different products without downtime.
5. Automated Stretch Wrapping
- Integrated Stretch Wrappers: Position automatic stretch wrappers directly at the end of the palletising line. By integrating stretch wrapping into the palletising process, pallets are wrapped immediately after they are formed, ensuring stability and reducing the need for additional manual handling. This seamless integration enhances overall efficiency and protects products during transport.
- Pre-Stretch Film: Utilise pre-stretch film in the wrapping process to enhance load stability while using less material. Pre-stretch film can stretch up to 250% before application, providing better coverage and load containment, which is essential for secure and stable pallets.
6. Monitoring and Preventative Maintenance
- Production Monitoring: Implement production monitoring systems to provide monitoring and control of the palletising process. This information will enable you to maintain efficiency, reduce downtime, and achieve higher product standards.
- Preventative maintenance: Ensure your equipment has a contract that includes regular service visits to ensure the equipment is maintained in good working order.
7. Operator Training and SOPs
- Standard Operating Procedures (SOPs): Develop comprehensive SOPs for all palletising tasks and ensure that all operators are trained to follow them. Clear and detailed SOPs help in standardising the process, reducing variability, and improving efficiency.
- Continuous Training Programs: Establish ongoing training programs to keep operators updated on the latest best practices, technologies, and safety protocols. Regular training ensures that operators are skilled and confident in using advanced equipment and following optimised procedures.
8. Lean Manufacturing Techniques
- Value Stream Mapping: Conduct value stream mapping specifically for the palletising process to identify and eliminate waste. This technique helps in visualising the entire process, pinpointing inefficiencies, and implementing targeted improvements. AMRs or AGVs can be used to ensure that the palletising system never has to stop and wait for pallets to be removed from the system.
- Kaizen Events: Organise regular Kaizen events focused on incremental improvements in the palletising area. These events encourage continuous improvement through collaborative efforts and can lead to significant enhancements in efficiency and productivity over time.
As you can see, there are many different strategies that can be implemented to speed up the palletising process in production. Not all of these may be applicable to your production environment, but implementing any of these strategies will ultimately enhance the speed and efficiency of your palletising process; leading to increased productivity, reduced operational costs, improved overall workflow, and a more competitive edge in the market.
If you would like to know more about the Granta palletising systems, then please do get in touch on 01223 499488 or contact us at helpline@granta-automation.co.uk. We will be very happy to help.
Warning: Undefined variable $aria_req in /var/www/granta-automation.co.uk/news/wp-content/themes/twentyten/comments.php on line 81
Warning: Undefined variable $aria_req in /var/www/granta-automation.co.uk/news/wp-content/themes/twentyten/comments.php on line 86